How Heat Tracing Systems Enhance Pipeline Safety: A Comprehensive Guide
How Heat Tracing Systems Enhance Pipeline Safety: A Comprehensive Guide
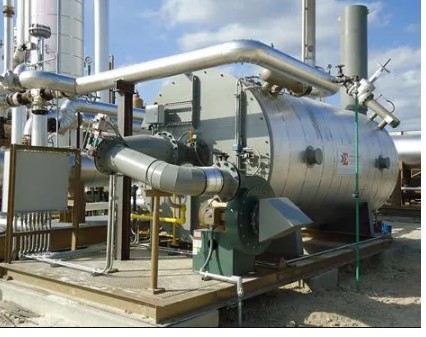
In the vast landscape of the oil and gas sector, safety remains paramount. Pipelines, the arteries of the industry, traverse great distances, carrying vital resources. Ensuring their integrity and reliability is not just a matter of operational efficiency but also a crucial element of environmental protection and human safety. In this context, heat tracing systems emerge as indispensable tools, offering a multifaceted approach to safeguarding pipelines against various risks. Let’s delve into the intricate ways in which heat tracing systems contribute to the safety and integrity of pipelines.
Understanding Heat Tracing Systems
Before delving into their safety implications, let’s grasp the fundamentals of heat tracing systems. Essentially, these systems involve the application of heat along the length of pipelines to maintain consistent temperatures. They come in various forms, including electric heat tracing, steam tracing, and hot water tracing. Each system is designed to prevent freezing, maintain viscosity, and control temperature fluctuations, thereby ensuring the smooth flow of materials within the pipelines.
Preventing Freezing and Hydrate Formation
One of the primary safety concerns in pipeline operations is the risk of freezing, especially in cold climates prevalent in regions like western Canada. Heat tracing systems mitigate this risk by continuously applying heat to the pipelines, preventing the formation of ice and hydrates. By maintaining temperatures above freezing levels, these systems ensure uninterrupted flow, averting potential blockages and operational disruptions.
Minimizing Corrosion and Material Degradation
Beyond freezing, temperature variations can also accelerate corrosion and material degradation in pipelines. Heat tracing systems play a crucial role in mitigating these risks by maintaining uniform temperatures. By preventing sudden temperature fluctuations, these systems help preserve the integrity of pipeline materials, extending their lifespan and reducing the likelihood of leaks or failures.
Ensuring Product Quality and Consistency
In industries like oil and gas, maintaining product quality is paramount. Temperature fluctuations within pipelines can compromise the integrity and characteristics of the materials being transported. Heat tracing systems ensure consistent temperatures, safeguarding the quality and properties of the products throughout the transportation process. This not only enhances operational efficiency but also ensures compliance with regulatory standards and customer expectations.
Facilitating Efficient Operation and Maintenance
Efficient operation and maintenance of pipelines are essential for ensuring safety and longevity. Heat tracing systems contribute to these objectives by facilitating easier monitoring and control of pipeline temperatures. Automated systems can adjust heat levels based on real-time data, optimizing energy consumption and minimizing operational costs. Moreover, proactive maintenance measures, such as periodic inspections and maintenance of heat tracing components, help identify and address potential issues before they escalate into safety hazards.
Enhancing Safety in Hazardous Environments
In addition to operational efficiency, heat tracing systems enhance safety in hazardous environments commonly found in the oil and gas sector. By preventing freezing and maintaining consistent temperatures, these systems reduce the risk of accidents such as leaks, spills, and explosions. Furthermore, in areas where combustible materials are present, such as oilfield buildings and vessels, heat tracing systems help mitigate the risk of fire by preventing the accumulation of flammable substances.
Supporting Regulatory Compliance
Regulatory compliance is a cornerstone of responsible pipeline management. Heat tracing systems play a pivotal role in meeting regulatory requirements related to pipeline safety and environmental protection. By implementing these systems, companies demonstrate their commitment to adherence to industry standards and regulations, thereby minimizing the risk of fines, penalties, and reputational damage.
Adapting to Diverse Applications and Environments
The versatility of heat tracing systems enables their application across a wide range of scenarios and environments within the oil and gas sector. Whether it’s insulating mechanical pipes, protecting oilfield buildings, or ensuring the integrity of vessels and tanks, heat tracing systems can be tailored to meet specific requirements. This adaptability makes them indispensable assets for addressing diverse safety challenges across different operational contexts.
Investing in Long-Term Sustainability
Beyond immediate safety benefits, the adoption of heat tracing systems aligns with long-term sustainability objectives within the oil and gas industry. By minimizing operational disruptions, reducing the risk of environmental contamination, and enhancing asset longevity, these systems contribute to the overall sustainability of pipeline infrastructure. Moreover, advancements in technology continue to improve the efficiency and environmental performance of heat tracing systems, further enhancing their sustainability credentials.
Conclusion: Harnessing The Power of Heat Tracing Systems for Pipeline Safety
In the dynamic landscape of the oil and gas sector, safety remains paramount. Heat tracing systems, expertly implemented by companies like G & R Insulating, emerge as invaluable tools for safeguarding pipeline integrity, mitigating operational risks, and ensuring regulatory compliance. From preventing freezing and corrosion to enhancing product quality and environmental stewardship, the benefits of these systems are far-reaching. By investing in G & R Insulating’s advanced heat tracing technology, companies can bolster their safety initiatives, optimize operational efficiency, and uphold their commitment to responsible pipeline management. As the industry continues to evolve, harnessing the power of G & R Insulating’s heat tracing systems will be essential for navigating the complexities of pipeline operations while prioritizing safety and sustainability.