The Essential Guide to Choosing the Right 3PL Warehouse Management System for Your Business
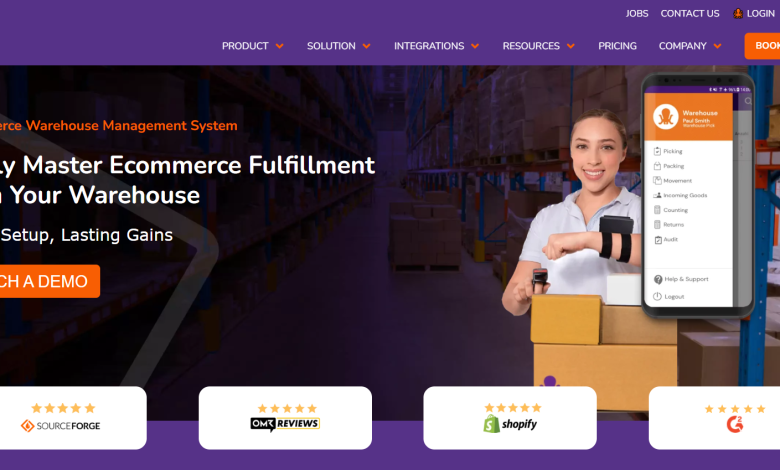
In today’s competitive business environment, efficient supply chain management is crucial for maintaining customer satisfaction and operational excellence. Third-party logistics (3PL) providers play a significant role in this process by offering specialized warehousing and distribution services. To maximize the benefits of partnering with a 3PL provider, it’s essential to implement the right warehouse management system (WMS). This article serves as an essential guide to choosing the right 3PL warehouse management system for your business, detailing the key factors to consider and providing actionable insights.
Understanding 3PL Warehouse Management Systems
A 3pl warehouse management system (WMS) is a software solution designed to manage and optimize warehouse operations for third-party logistics providers. Unlike traditional WMS solutions, a 3PL WMS caters to the complexities of managing inventory and fulfilling orders for multiple clients simultaneously. It integrates various functions, such as inventory tracking, order management, and shipping logistics, to streamline warehouse processes and enhance overall efficiency.
Key Factors to Consider When Choosing a 3PL WMS
Selecting the right 3PL WMS involves evaluating several critical factors to ensure that the system aligns with your business needs and operational requirements. Here are the key considerations:
1. Integration Capabilities
Why It Matters: Integration is essential for seamless operations and data consistency. The 3PL WMS should integrate smoothly with your existing business systems, including enterprise resource planning (ERP), customer relationship management (CRM), and ecommerce platforms.
What to Look For:
- Compatibility: Ensure the WMS can interface with your current systems without requiring extensive customization.
- API Availability: Check for robust application programming interfaces (APIs) that facilitate data exchange and integration.
- Vendor Support: Verify that the WMS vendor provides support for integration with various third-party systems.
2. Feature Set
Why It Matters: The features offered by a 3PL WMS determine how well it can meet your specific operational needs. A comprehensive feature set can enhance efficiency, accuracy, and overall warehouse performance.
Key Features to Consider:
- Real-Time Inventory Tracking: Enables up-to-date visibility of inventory levels and locations.
- Order Management: Automates order processing, picking, packing, and shipping.
- Warehouse Layout Optimization: Helps design and manage warehouse layouts for optimal space utilization and workflow efficiency.
- Reporting and Analytics: Provides insights into operational performance, inventory levels, and order fulfillment metrics.
- Barcode Scanning and RFID: Supports accurate item tracking and verification through scanning technologies.
3. Scalability and Flexibility
Why It Matters: As your business grows and evolves, your 3PL WMS needs to scale with it. A scalable and flexible system can accommodate increasing order volumes, expanding inventory, and changing operational requirements.
What to Look For:
- Modular Design: Choose a WMS with modular capabilities that allow you to add or adjust features as needed.
- Performance Metrics: Ensure the system can handle higher transaction volumes and complex operations.
- Customization Options: Look for a WMS that offers customization to fit your unique business processes.
4. User-Friendliness
Why It Matters: A user-friendly interface reduces the learning curve for warehouse staff and minimizes the risk of errors. The system should be intuitive and easy to navigate to enhance productivity and reduce training time.
What to Look For:
- Interface Design: Select a WMS with a clean, intuitive user interface that simplifies daily tasks.
- Training Resources: Ensure that the vendor provides comprehensive training materials and support for users.
- Ease of Use: Opt for a system that minimizes complexity and allows users to perform tasks efficiently.
5. Cost and Return on Investment (ROI)
Why It Matters: Cost is a significant factor in choosing a 3PL WMS, but it’s essential to consider the return on investment (ROI) as well. While a lower initial cost may be appealing, it’s crucial to evaluate the long-term benefits and savings provided by the system.
What to Look For:
- Total Cost of Ownership: Assess the total cost, including licensing fees, implementation costs, and ongoing maintenance.
- Cost-Benefit Analysis: Evaluate the potential ROI based on improved efficiency, reduced errors, and enhanced customer satisfaction.
- Flexible Pricing Models: Consider WMS providers that offer flexible pricing options, such as subscription-based models or pay-as-you-go plans.
6. Support and Training
Why It Matters: Effective support and training are critical for ensuring that your team can fully utilize the WMS and address any issues that arise. Reliable support can prevent disruptions and help resolve problems quickly.
What to Look For:
- Customer Support: Verify that the vendor offers responsive and accessible customer support services.
- Training Programs: Ensure that comprehensive training programs are available to help your team get up to speed with the system.
- Documentation: Look for detailed documentation and user guides that provide additional support and reference materials.
7. Security and Compliance
Why It Matters: Security and compliance are crucial for protecting sensitive data and ensuring adherence to industry regulations. The WMS should include robust security features to safeguard your information and operations.
What to Look For:
- Data Encryption: Ensure that the system employs encryption to protect data during transmission and storage.
- Access Controls: Check for customizable access controls to restrict system access based on user roles and responsibilities.
- Compliance: Verify that the WMS complies with industry standards and regulations, such as GDPR or PCI-DSS, if applicable.
Steps to Selecting the Right 3PL WMS
To ensure that you choose the right 3PL WMS for your business, follow these steps:
1. Define Your Requirements
Start by outlining your specific needs and goals for the WMS. Consider factors such as the size of your warehouse, the complexity of your operations, and any unique requirements you may have.
2. Research and Compare Solutions
Conduct thorough research on available WMS solutions and compare their features, capabilities, and pricing. Look for reviews, case studies, and testimonials from other businesses in your industry.
3. Request Demos and Trials
Request demonstrations and trials of shortlisted WMS solutions to see how they perform in real-world scenarios. Evaluate the ease of use, functionality, and integration capabilities during these trials.
4. Evaluate Vendor Support
Assess the level of support and training provided by the vendor. Ensure that they offer adequate resources to help you implement and maintain the system effectively.
5. Make an Informed Decision
Based on your research, trials, and evaluations, make an informed decision on the WMS that best aligns with your business needs and goals. Consider the long-term benefits and ROI when making your final choice.
Conclusion
Choosing the right 3PL warehouse management system is a critical decision that can significantly impact your logistics and supply chain operations. By carefully evaluating factors such as integration capabilities, feature set, scalability, user-friendliness, cost, support, and security, you can select a WMS that enhances efficiency, accuracy, and overall performance.
A well-chosen 3PL WMS will streamline warehouse operations, improve order fulfillment, and contribute to greater customer satisfaction. As you navigate the selection process, focus on finding a solution that aligns with your specific requirements and supports your business’s growth and success. By making an informed decision, you can leverage the power of technology to optimize your logistics operations and stay competitive in the ever-evolving market.