7 Compelling Reasons Why 3D Printed Bands and Rpes Are Revolutionizing Industries
7 Compelling Reasons Why 3D Printed Bands and Rpes Are Revolutionizing Industries
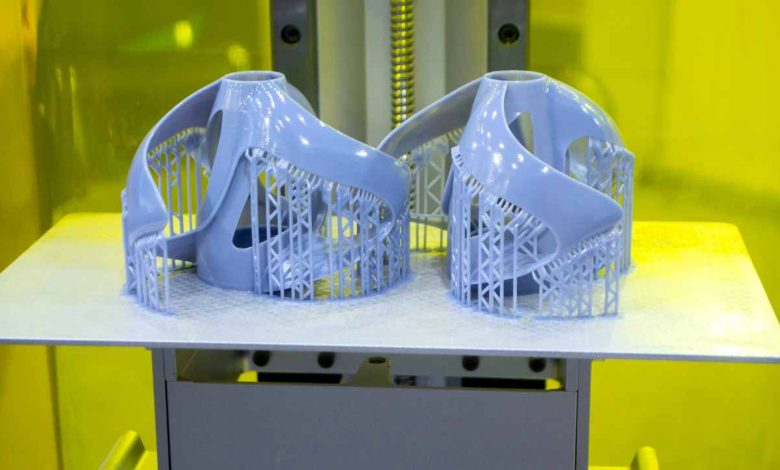
In recent years, the advent of 3D printing technology has brought about a paradigm shift in various industries. One of the most notable applications of this technology is in the creation of 3D printed bands and rpes. From healthcare to fashion, the versatility and innovation of 3D printed bands and rpes have been reshaping traditional processes and unlocking new possibilities. In this article, we delve into the world of 3D printed bands and rpes, exploring their significance, applications, and future implications.
3D Printed Bands and Rpes: Redefining Manufacturing
3D printing, also known as additive manufacturing, has emerged as a game-changer in the manufacturing landscape. Unlike conventional manufacturing methods that involve subtractive processes, such as cutting or drilling, 3D printing builds objects layer by layer, allowing for intricate designs and customized products. 3D printed bands and rpes exemplify this transformative approach, offering unparalleled flexibility and precision in their production.
The Evolution of 3D Printing Technology
The journey of 3D printed bands and rpes traces back to the evolution of 3D printing technology itself. Initially used for rapid prototyping, 3D printing has evolved into a sophisticated manufacturing technique capable of producing end-use products with high strength and durability. The advancements in materials, printing processes, and design software have propelled the adoption of 3D printed bands and rpes across various industries.
Applications of 3D Printed Bands and Rpes
The applications of 3D printed bands and rpes span across a multitude of industries, showcasing the versatility and adaptability of this technology. In healthcare, 3D printed bands find applications in prosthetics, orthodontics, and surgical instrumentation, offering personalized solutions and improved patient outcomes. Similarly, in the fashion industry, 3D printed rpes enable designers to create avant-garde accessories and garments, pushing the boundaries of creativity and sustainability.
Advantages of 3D Printed Bands and Rpes
The adoption of 3D printed bands and rpes brings forth a myriad of advantages, driving efficiency, innovation, and cost-effectiveness. Unlike traditional manufacturing methods that often involve lengthy lead times and high production costs, 3D printing offers rapid prototyping and on-demand production, reducing time-to-market and minimizing waste. Additionally, the ability to customize designs and tailor products to specific requirements enhances functionality and user experience.
Challenges and Future Directions
While the potential of 3D printed bands and rpes is vast, it is not without its challenges. Technical limitations, material properties, and regulatory considerations pose obstacles to widespread adoption and scalability. However, ongoing research and development efforts are addressing these challenges, paving the way for further advancements and breakthroughs in the field of additive manufacturing.
FAQs
1. Are 3D printed bands and rpes durable? Yes, 3D printed bands and rpes can be highly durable, depending on the materials used and the printing parameters optimized for strength.
2. Can 3D printed bands and rpes be customized? Absolutely! One of the key advantages of 3D printing is its ability to customize designs, allowing for tailored solutions to meet specific needs and preferences.
3. How does 3D printing contribute to sustainability? 3D printing minimizes material wastage by only using the amount of material required for the object, thus reducing environmental impact compared to traditional manufacturing methods.
4. What industries can benefit from 3D printed bands and rpes? Various industries, including healthcare, fashion, automotive, aerospace, and consumer goods, can benefit from the innovative applications of 3D printed bands and rpes.
5. Is 3D printing technology expensive to implement? While initial investments in 3D printing technology may be significant, the long-term cost savings, efficiency gains, and innovation opportunities outweigh the upfront costs for many businesses.
6. Are there any limitations to the size of objects that can be 3D printed? Yes, the size of objects that can be 3D printed is limited by the build volume of the 3D printer. However, advancements in printer technology are expanding the possibilities for larger-scale printing.
Conclusion
In conclusion, 3D printed bands and rpes represent a revolutionary advancement in manufacturing technology, offering unprecedented levels of customization, efficiency, and innovation. From healthcare to fashion, the impact of 3D printed bands and rpes is reshaping industries and unlocking new possibilities for design and production. As technology continues to evolve and barriers are overcome, the future holds endless opportunities for the widespread adoption and integration of 3D printed bands and rpes into everyday life.